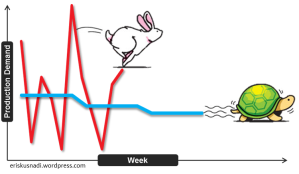
Artikel "Heijunka dalam Penjadwalan Produksi" ini kami ambil dari tulisan Eris Kusnadi semoga bisa menambah wawasan para pemabaca :
Ohno (1988) : “The slower but consistent tortoise causes less waste and is much more desirable than the speedy hare that races ahead and then stops occasionally to doze” (Liker, 2004, Chap.10)
Keunggulan filosofi Jepang diumpamakan seperti perlombaan antara kelinci dan kura-kura. Ohno membuat cerita: kura-kura yang lamban namun konsisten mengakibatkan lebih sedikit pemborosan dan jauh lebih diinginkan daripada kelinci yang cepat dan unggul dalam perlombaan dan kemudian berhenti karena adakalanya mengantuk (Liker, 2004, chap. 10).
Ini merupakan suatu ilustrasi prinsip perataan (leveling) di mana beban kerja diratakan demi kesinambungan (konsistensi kura-kura) dengan tanpa melihat variasi pesanan (kecepatan kelinci). Ohno kemudian melanjutkan ceritanya bahwa Toyota Production System (TPS) hanya dapat direalisasikan jika semua orang menjadi kura-kura yang lamban dan mantap daripada lari cepat dan tersentak-sentak seperti kelinci, seperti pada sistem produksi tradisional.
Tujuan TPS adalah membangun sistem yang ramping (lean), hal itu dapat diusahakan dengan memproduksi barang tepat ketika diinginkan pelanggan, just-in-time (JIT)! Namun, permintaan pada kenyataannya sangat sulit diprediksi dan pesanan aktual umumnya bervariasi dari waktu ke waktu. Misal kita membuat produk karena adanya pesanan dan jumlah pesanan tersebut besar, mungkin kita membuat produk dengan jumlah yang besar untuk satu periode yang menyebabkan pekerja dan peralatan harus bekerja keras dan berakibat pada tingginya risiko. Kemudian pada periode berikutnya, jumlah pesanan kecil maka pekerjaan menjadi sedikit dan peralatan menjadi kurang bermanfaat (underutilized). Kita juga tidak tahu berapa banyak material yang harus dipesan sehingga terpaksa harus menumpuk material.
Produksi berdasarkan pesanan tidak menjamin suatu sistem yang ramping. Seperti uraian di atas, cara tersebut justru menimbulkan kondisi yang tidak teratur (mura) yang akhirnya memunculkan beberapa pemborosan atau “muda” (e.g. lembur, persediaan, biaya ekspres pasokan/ pengiriman, stress pekerja, etc.). TPS menyiasati hal tersebut dengan meratakan beban dan tidak selalu memproduksi berdasarkan pesanan. Konsep ini dikenal sebagaiheijunka; yang berdasarkan uraian di atas, dapat diartikan sebagai distribusi pemerataan volume produksi dan baurannya.
Dalam bahasa Inggris, heijunka memiliki dua arti berbeda, tetapi saling berhubungan. Yang pertama adalah: leveling of production by volume yang berarti perataan volume atau jadwal produksi, selanjutnya dalam bahasan ini akan disebut production leveling. Dan kedua, leveling production by product type or mix yang berarti perataan tipe atau bauran produk dalam jadwal produksi, selanjutnya dalam bahasan ini akan disebut product leveling. Hubungan keduanya dapat tergambar pada penjelasan teknis masing-masing, yang akan dibahas pada bab selanjutnya.
I. Production Leveling
JIT yang ideal adalah sangat sulit karena respon yang benar-benar JIT untuk fluktuasi permintaan pelanggan dapat mengakibatkan terjadinya lembur (bila fluktuasi naik) atau waktu menganggur (bila fluktuasi turun). Selain itu, jadwal produksinya dapat membuat pekerja stress. Production leveling mencoba mengatasi masalah ini. Sebagai ilustrasi, berikut suatu contoh produksi JIT dan production leveling (Tabel 1):
Dari Gambar 1 diketahui bahwa ciri-ciri JIT, diantaranya:
- memenuhi permintaan pelanggan tepat ketika ada permintaan (just-in-time);
- mengurangi persediaan barang jadi (finished goods);
- jadwal kerja tidak dapat diramalkan; dan
- pemasok yang berada di hulu (upstreams) harus mempunyai variabilitas yang tinggi demi memenuhi variasi permintaan pelanggan.
Dan, ciri-ciri production leveling, diantaranya:
- memenuhi total permintaan pelanggan berdasarkan periode production leveling yang ditentukan (pada kasus di atas dalam mingguan);
- persediaan barang jadi (finished goods) dibuat untuk periode jangka pendek yang memiliki permintaan tinggi;
- jadwal kerja dapat diramalkan; dan
- kestabilan produksi ditransmisikan keseluruh rantai pasokan (supply chain) untuk mengurangi persediaan pemasok.
II. Product Leveling
Ukuran produksi yang besar dari produk yang sama memang dapat mereduksisetup time (waktu penyiapan peralatan, etc.) dan changeover time (waktu pergantian sistem, produk, etc.), tetapi umumnya mengakibatkan: (a) waktu tunggu operasi (lead time) yang panjang, (b) pembengkakan persediaan, (c) kemungkinan cacat produk yang besar, dan (d) waktu menganggur (idle time) dan lembur yang berlebihan.
Apabila suatu produk lebih dari satu tipe maka product leveling adalah cara kritis untuk menghindari akibat-akibat di atas, sebagai ilustrasi lihat Gambar 1.
Untuk memudahkan pemahaman teknisnya, kita akan menggunakan suatu contoh kasus sederhana, yaitu sebagai berikut:
Suatu pabrik akan memproduksi:
- Produk X sebanyak 1.000 unit per bulan,
- Produk Y sebanyak 600 unit per bulan, dan
- Produk Z sebanyak 400 unit per bulan.
Waktu kerja = 8 jam (28.800 detik) dalam sehari, 5 hari dalam seminggu, dan 20 hari dalam sebulan.Produksi harian = (1.000 + 600 + 400) ÷ 20 hari = 100 unit per hari.
Waktu untuk membuat 1 unit produk = 28.800 detik ÷ 100 unit per hari = 288 detik per unit.
Berikut langkah-langkah teknis product leveling:
2.1 Pendekatan Pertama: Perencanaan Tradisional
Pendekatan umum dalam produksi massal adalah mengoptimalkan penggunaan sumber-sumber daya dan mencoba skala penghematan dengan ukuran produksi sangat besar karena ukuran besar berakibat pada waktu kechangeover lama sehingga banyaknya changeover minimal.
Praktek umum lain adalah memulai bulan dengan rangkaian produksi yang panjang dan membiarkan rangkaian produksi yang pendek di akhir bulan. Ini terjadi oleh karena adanya kepercayaan bahwa rangkaian yang lebih besar adalah penting dan tidak memiliki risiko gangguan.
Gambar 2 memperlihatkan jadwal produksi (kasus produk X, Y, dan Z) dengan menggunakan pendekatan tradisional. Tampak bahwa produk Y dan Z tidak memiliki persediaan (out of stock) pada minggu ke-1 dan minggu ke-2. Apabila pelanggan memesan:
- 1 unit X,
- 1 unit Y, dan
- 1 unit Z
pada hari pertama pada bulan itu maka pelanggan harus menunggu produk Z diselesaikan (±17 hari kerja). Sebagai ukuran (untuk perbandingan), kita menggunakan rasio usable time per total time, yaitu:
(Usable time) ÷ (Total time) = (3 tipe x 288 detik per unit) ÷ (17 hari x 28.800 detik) = 0,18%.
2.2 Perbaikan Pertama: Basis Mingguan
Jika suatu perbaikan sistem dilakukan sehingga jadwal produksi dapat diratakan ke dalam basis mingguan maka pelanggan cukup menunggu 5 hari (lihat Gambar 3).
Rasio usable time per total time adalah: (3 x 288) ÷ (5 x 28.800) = 0,60%.
2.3 Perbaikan Lanjutan: Basis Harian
Bayangkan apabila suatu perbaikan lagi dapat dilakukan sehingga kita dapat meratakan jadwal produksi ke dalam basis harian maka pelanggan hanya cukup menunggu satu hari (lihat Gambar 4).
Rasio usable time per total time adalah: (3 x 288) ÷ (1 x 28.800) = 3%.
2.4 Mencari Pola atau Sekuen Product Leveling
Dalam sistem TPS, pelanggan biasanya meminta pengiriman lebih dari satu kali dalam sehari, tujuannya adalah untuk meminimalkan persediaan. Seandainya terdapat permintaan harian pelanggan sebesar 100 unit per hari, mungkin pelanggan akan meminta dikirim 10 unit sebanyak 10 kali pengiriman dalam sehari (sesuai jadwal yang telah disepakati).
Oleh karena itu, perbaikan waktu diperlukan untuk mempertahankan pasar dan memperoleh fleksibilitas, caranya adalah dengan membagi batchmelalui pencarian suatu sekuen atau pola rangkaian/susunan produk yang sesuai untuk jangka waktu yang lebih kecil (harian atau lebih kecil lagi) kemudian sekuen ini akan diulang terus sampai keseluruhan permintaan (bulanan) tercukupi. Hal ini berarti mencari suatu kompromi antara ukuranbatch minimum, sisi biaya, dan upaya changeover dan skala penghematan batch besar. Konsep product leveling sangat relevan bagi lingkungan manufaktur repetitif seperti ini (TPS). Berikut akan diterangkan bagaimana langkah-langkah teknisnya:
Tahap 1: menentukan total minimum unit dalam sebuah sekuen produk pada satu sekuen waktu (total minimum number of units in a sequence to the sequence time). Berikut langkah-langkahnya :
Tahap 1.1: menentukan product cycle time, yaitu sebagai berikut:
- CT Produk X: 28.800 detik ÷ 50 unit per hari = 576 detik per unit
- CT Produk Y: 28.800 detik ÷ 30 unit per hari = 960 detik per unit
- CT Produk Z: 28.800 detik ÷ 20 unit per hari = 1.440 detik per unit
Tahap 1.2: menentukan pacu kerja atau takt time (TT) penyelesaian satu unit produk.
- Jumlah produk yang diproses dalam sehari = 50 + 30 + 20 = 100 unit.
- TT = 28.800 ÷ 100 = 288 detik per satu unit.
Artinya, satu unit ini merepresentasikan 0,5 unit X; 0,3 unit Y; dan 0,2 unit Z (288 detik ÷ CT Produk).
Tahap 1.3: menentukan ukuran sekuen minimum. Apabila manufaktur menyediakan waktu 1.745 detik untuk satu kali sekuen, maka:
- Ukuran sekuen = 1.745 ÷ 288 = 6 unit, dengan kombinasi 3 unit X, 2 unit Y, dan 1 unit Z.
- Ukuran sekuen 6 unit akan diulang: 28.800 detik ÷ 1.745 detik = 16,5 kali.
Tahap 2: penjadwalan, caranya adalah menempatkan X, Y, dan Z pada satu sekuen secara merata. Berikut caranya:
Tahap 2.1: tempatkan X (3 unit) terlebih dahulu, diusahakan penempatan berselang-seling:
Tahap 2.2: sel yang masih kosong diisi dengan Y kemudian Z:
Tahap 2.3: sekuen di atas akan diulang 16,5 kali (lihat Gambar 5).
.
Dengan cara ini, pelanggan hanya menunggu ±29 menit (1.745 detik atau 0,06 hari) untuk memperoleh produk dari masing-masing tipe.
Rasio usable time ÷ total time adalah: (3 x 288) ÷ (0,06 x 28.800) = 49,51%.
Dalam prakteknya, penempatan pesanan/ kanban di heijunka box adalah ditentukan konsumen, tetapi dengan tetap mempertimbangkan pemerataan beban kerja.
III. Penutup
Dengan heijunka, semua pelanggan–siapapun dia dan berapa pun jumlah pesanannya–akan selalu diperhitungkan (berapa pun jumlah pesanan akan selalu ada dalam periodisasi yang lebih pendek). Hal ini menjaga kesinambungan rantai pasok dan memberikan pelayanan yang lebih baik sehingga semua pelanggan merasa terpuaskan dan tidak akan pindah ke perusahaan lain.
Heijunka membuat stabilitas (ketenangan) dalam proses manufaktur. Tanpa heijunka, perusahaan dan mitra anda tidak akan tenang dan tersenyum seperti ini!
Rujukan:
0 Response to "Heijunka dalam Penjadwalan Produksi"
Posting Komentar